Custom Equipment Design & Automation
We know your needs and technical specifications; we will turn it into real equipment that helps you to accomplish your task!
IDEAS and MODELLING… we study hard and work hard for potential errors that might inherit in the conceptual work, GET IT RIGHT THE FIRST TIME!
Fully Automatic Liquid Polymer Casting Machine
Turning ideas into reality that works!
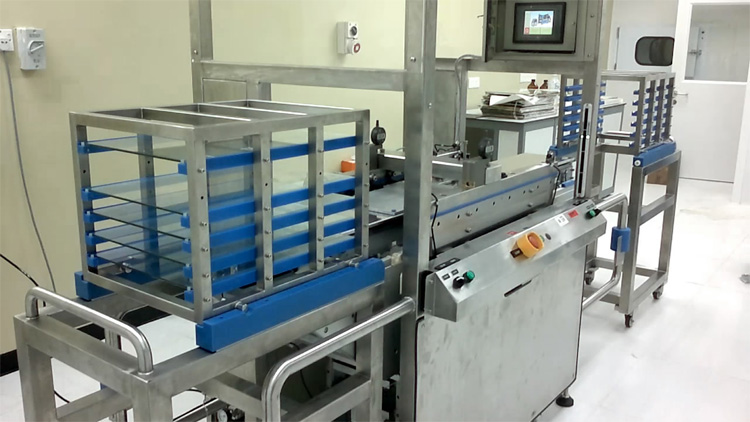
Machine specifications:
- When the glass is transfer on to the Casting Platform, the stopper and guide on the platform will place the glass at the desired location.
- Hold the glass firmly on the platform.
- The Casting Platform will move toward the Casting Section.
- Casting solution is pour into the Solution Reservoir (length of 300mm, reservoir’s volume up to 1000 mL of casting solution) with different opening width (0.3mm, 0.5mm, 0.75mm, 1mm and 2mm) for different viscosity of casting solution.
- The Solution Reservoir (length of 300mm) will coat the material on to the glass.
- The Casting Blade will cast a thin layer of material on the glass. The thickness of the material is preset.
- The coated glass is being push to the Conveyor of the Unloader
- 3 Variables can be controlled:
- The Volume of the material that being injected (up to 1000 mL)
- The Casting Speed (10 mm/s up to 100 mm/s)
- The thickness of the material (0.05 mm to 0.8 mm), interval thickness adjustment of 0.005mm.
- Pressurized dispenser
- Conveyor at 2m/min with adjustable speed, max room length=7m
- thickness controller blade with measuring display
- Dispenser Unit
- Featuring multichannel flow to ensure even dispensing over 300mm width
- Material: SUS 316/ Perspex at side for viewing
- Solution Container with cover
- Solution Reservoir (length of 300mm, reservoir’s volume up to 1000 mL of casting solution) with different opening width (0.3mm, 0.5mm, 0.75mm, 1mm and 2mm) for different viscosity of casting solution
- 5 pieces of Doctor blade will be provided
- Tolerance : ± 5 micron
Temperature and pressure tester for quality control
![]() |
|
Actual machine in operation after buy off
Logo Patent Polishing Machine
![]() |
|
Fully automated plastic thin film removal machine
Serving Agricultural Industry
Sugarcane chopping machine
Due to intensive labor hour of the chopping sugarcane into its custom length for export, foreign working not able to work long hours to complete the commited output on demand.
This machine greatly reduces the fatigue of man power and further more lower the dependency of foreign workers.
Specification
- Fully pneumatic control and activation
- Manual insertion of sugarcane onto safely concealed compartment for chopping.
- Pneumatic rocker arm action (top down) for chopping with manual safety switch for short length chopping.
- 2 sugarcane length setting sensor activated by pneumatic valve plate.
- Adjustable location guide for sugarcane feeding.
- Standalone concealed chopping module from the main frame for easy maintenance and servicing.
- Low blade operating profile and isolated pneumatic filtering unit from processing compartment.
- Minimum modified chopping knife easy to change knife holder for maintenance.
- End product as of current 1st prototype quality is acceptable. Cutting angle of 35 degree with lower edge of the 2 parallel edges as reference. Rough cutting surface and minor skin residue might be unavoidable.
Simple semi-automatic counter
|
![]() |